Bau einer Versuchsstrecke in Mainz-Amöneburg
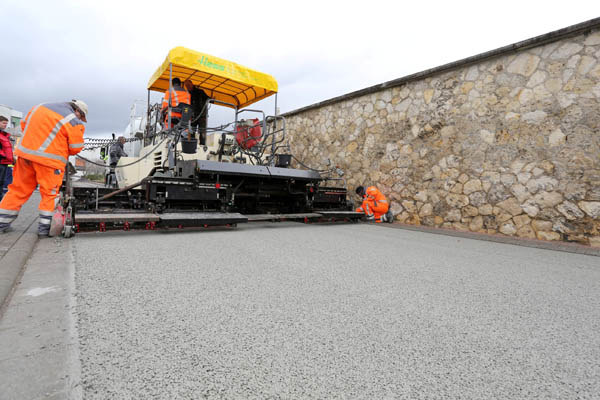
Beim Einbau des Dränbetons kam ein modifizierter Asphalt-Straßenfertiger zum Einsatz.
Ob PKW-Parkplätze vor großen Verbrauchermärkten, Wohngebietsstraßen, Radwege oder Gleisbereiche von Straßenbahnen: Die meisten Verkehrsflächen werden in Deutschland noch immer mit Asphaltdecke ausgeführt. Das könnte sich jedoch zukünftig ändern. Denn auf dem Werksgelände der Dyckerhoff AG in Mainz-Amöneburg wurde im Rahmen eines umfangreichen Praxistests eine Versuchsstraße mit einer Decke aus polymermodifiziertem offenporigen Dränbeton ausgeführt. Das Pilotprojekt stellt die Vorteile und die Praxistauglichkeit der Dränbeton-Bauweise unter Beweis und wird in Kürze als Referenz in das Merkblatt „Versickerungsfähige Verkehrsflächen“ der Forschungsgesellschaft für Straßen- und Verkehrswesen e.V. (FGSV) aufgenommen.
Überzeugende Vorteile Dr. Reinhard Winzer aus dem Produktmarketing der Dyckerhoff AG – als Leiter der Betreuungsgruppe „Dränbeton“ der Forschungsgemeinschaft Transportbeton e.V. (FTB) an der Ausarbeitung des neuen Beton-Merkblatts beteiligt – erklärt: „Offenporiger, wasserdurchlässiger Beton als Deckschicht im Straßenbau weist eine Reihe von Vorteilen auf. Die größeren, untereinander verbundenen Hohlräume, die im erhärteten Dränbeton entstehen, ermöglichen sowohl eine dauerhafte Abführung des Niederschlagwassers als auch eine deutliche Lärmminderung. Die bereits bekannte Bauweise aus offenporigem Beton – OPB genannt – wird bei Autobahnen und Schnellstraßen erfolgreich eingesetzt und ermöglicht dort vor allem eine deutliche Lärmreduktion. Im kommunalen Bereich liegen jedoch für den Dränbeton noch enorme Potenziale – ob als versickerungsfähige Verkehrsflächen für Stadt- und Gemeindestraßen, Gleisbereiche von Straßenbahnen oder im ländlichen Wegebau. Denn im Vergleich zur üblichen Asphalt- oder Pflasterbauweise lässt sich damit die unnötige Versiegelung von Verkehrsflächen nachhaltig vermeiden. Das entlastet Kanalnetze und mindert Überschwemmungen“.
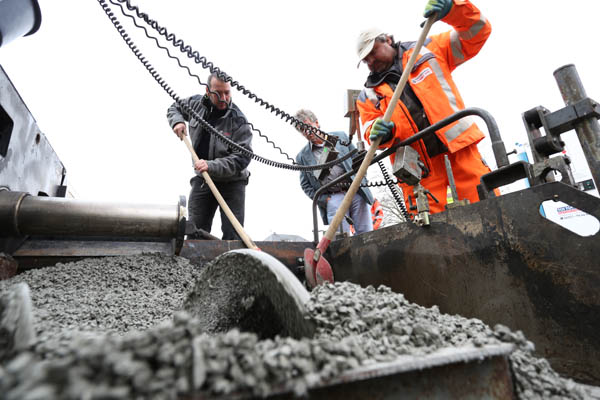
Den Einbau des Betons übernahm eine Asphaltstraßenbaukolonne.
Die Teststrecke im Detail: Aufbau und Produktion Die kürzlich auf dem Werksgelände der Dyckerhoff AG erstellte Versuchsstraße ist ca. 130 Meter lang und 4,90 Meter breit. Die Straße dient der Zu- und Abfahrt von PKWs zum Parkplatz mit über 300 Stellplätzen, darüber hinaus verkehren hier LKW und Busse. So entspricht die Belastungsklasse mindestens der einer Wohngebietsstraße gemäß den Richtlinien für die Standardisierung des Oberbaues von Verkehrsflächen (RStO). Zum Straßenaufbau: Auf eine wasserdurchlässige Tragschicht ohne Bindemittel (ToB) wurde der Dränbeton mit einer Dicke von 23 Zentimetern aufgebracht. Dabei wurde auf einer Länge von ca. 65 Metern ein Beton mit CEM III/A 42,5 N verwendet und auf den weiteren ca. 65 Metern der Teststrecke ein Beton mit CEM II/ B-S 52,5 R eingesetzt – jeweils mit der Polymerdispersion Etonis der Wacker Chemie versetzt. Die Rezeptur wurde vom Wilhelm Dyckerhoff Institut (WDI) in enger Zusammenarbeit mit Wacker Chemie entwickelt und in Tests und Laborversuchen umfassend geprüft. Mit der unabhängigen Überwachung von Produktion, Einbau und Langzeittauglichkeit der Teststrecke beauftragte die FTB Beton-Experte Prof. Dr.-Ing. Udo Hinterwäller von der Fachhochschule Frankfurt a. Main.
Ausführung der Teststrecke Produziert wurde im Dyckerhoff Transportbetonwerk Rhein-Main-Taunus. Paul Vogel, Leiter der Anwendungstechnik im Wilhelm-Dyckerhoff-Institut und Projektleiter bei Dyckerhoff: „Da Dränbeton mit normaler Misch- und Dosiertechnik hergestellt und mit üblichen Fahrzeugen transportiert werden kann, ist er problemlos flächendeckend in ganz Deutschland verfügbar“. Den Einbau des Betons übernahm eine Asphaltstraßenbaukolonne der Bauunternehmung Albert Weil AG (Limburg-Offheim), die im Vorfeld einen halben Tag geschult wurde. Als Einbaugerät kam ein modifizierter Asphalt-Straßenfertiger zum Einsatz. „Eine Besonderheit ist die variabel auf die Straßenbreite einstellbare Ausziehbohle“, erläutert Anwendungstechniker Dieter Schwenninger. „Durch eine Veränderung der Geometrie der Bohlenteile wurden außerdem die Auflageflächen so dimensioniert, dass auf dem Belag keine nachteiligen Bohlenabdrücke zustande kommen. Darüber hinaus haben wir die Anordnung der Verdichtungselemente so variiert, dass auch die 23 Zentimeter dicke Betonschicht ausschließlich mit Tampertechnik verdichtet werden konnte. Um ein Absinken der Bohle zu verhindern, wurde schließlich an beiden Seiten des Straßenfertigers ein Rollensystem angebracht“. Durch die gut verarbeitbare Konsistenz des Dränbetons ließen sich auf der gesamten Teststrecke sehr ebene Oberflächen realisieren. Auch die höhenmäßige Anpassung der Schachtringe und Hydrantenschieber in der Straße waren per Hand in hoher Qualität ausführbar. Seit April wird die Teststrecke nun genutzt und im Rahmen einer Langzeitstudie kontinuierlich weiter analysiert. Dr. Olaf Aßbrock, Geschäftsführer des Bundesverbands Transportbeton und einer der Impulsgeber zur Anlage der Teststrecke zeigt sich sehr zufrieden: „Das Testprojekt zeigt eindrucksvoll, dass Dränbeton im Straßenbau zahlreiche Vorteile gegenüber herkömmlichen Bauweisen mit Asphalt aufweist. Auch die Betonproduktion, die Logistik und die Einbringung des Betons ist mit bestehender Technik möglich. Daher sehen wir für den Dränbeton in Deutschland große Potenziale, vor allem wenn es um die Herstellung versickerungsfähiger Verkehrsflächen für PKW-Parkplätze und Wohngebietsstraßen geht“.
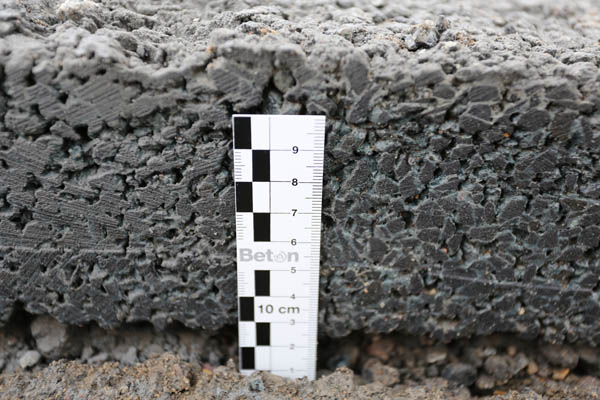
Offenporiger, wasserdurchlässiger Beton als Deckschicht im Detail.
Fotos: BetonBild |