Der perfekte Fertiger für ein komplexes Großprojekt
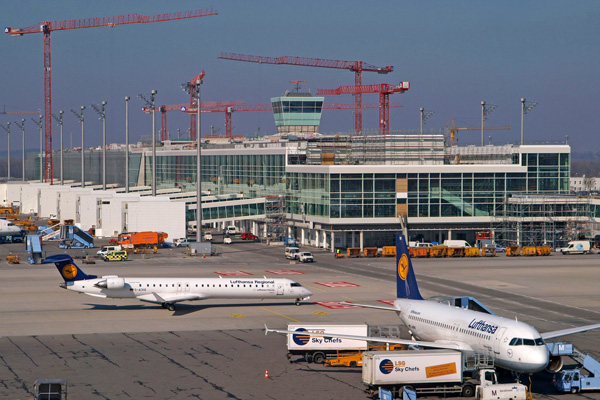
Das künftige Satellitengebäude für das Terminal 2 nimmt zunehmend Gestalt an: Die Arbeiten an der Fassade und im Zentralbereich sind bereits weit fortgeschritten, nach und nach werden die Stege für die 27 Fluggastbrücken eingehängt. Es ist bereits gut zu erkennen, wie der Vorfeldtower in das Gebäude integriert wird. Die Abfertigungskapazität des Münchner Flughafens steigt durch das Satellitengebäude um rund elf Millionen Passagiere pro Jahr.
BU und Pressefoto: Flughafen München GmbH
Eines der wichtigsten Großprojekte vor den Toren Münchens ist der Bau eines Satellitenterminals als Erweiterung des Terminals 2 am Flughafen München. Auf dem Vorfeld Ost sollen künftig zusätzlich elf Millionen Fluggäste abgefertigt werden. Für die 76.000 m2 große Vorfeldfläche setzt die Arge Streicher-Berger den Fertiger BF 800 C von Bomag zum Einbau der hydraulisch gebundenen Tragschicht ein. Projekteiter Walter Weinberger zeigt sich begeistert von der Einsparung von Kosten und Arbeitszeit durch die Verwendung von UTS-Daten aus der 3D-Planung.
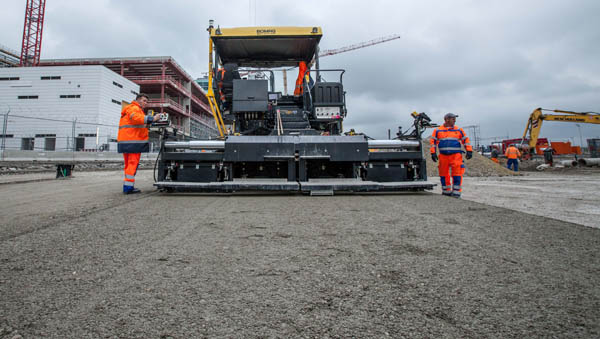
Der BF 800 C mit der S 500 Hochleistungsbohle sorgt für optimale Einbauergebnisse – auch unter erschwerten Bedingungen.
Der Flughafen München hat sich im Kreis der großen europäischen Luftverkehrsdrehkreuze etabliert und sorgt nun mit Blick auf die stetig steigenden Fluggastzahlen gemeinsam mit der Deutschen Lufthansa für zusätzliche Kapazitäten im Bereich der Passagierabfertigung. Deshalb wird die Abfertigungskapazität des Terminals 2 durch einen parallel verlaufenden Satelliten nach Osten erweitert. Hier sollen, mit geplanter baulicher Fertigstellung im Jahr 2015, sowohl 27 kleinere als auch größere Flugzeuge wie der Airbus A 380 abgefertigt werden. Damit wächst die Kapazität von derzeit 25 Millionen Passagieren im Jahr bereits im ersten Bauabschnitt um rund 11 Millionen. Derzeit ist alles noch eine Baustelle, die vom eigentlichen Vorfeld mit Flugbetrieb abgekoppelt ist. Später wird der Satellit über ein unterirdisches Personentransportsystem mit dem Terminal 2 verbunden.
Anfang April 2013 bekam die Bietergemeinschaft Streicher-Berger den Auftrag zur Erneuerung des Vorfeldes Ost am Münchner Flughafen. Das Vorfeld umfasst eine Fläche von ca. 76.000 m² und bietet Parkpositionen für die Flugzeuge.
Die Fläche wird in zwei Abschnitten wieder hergestellt: • Abschnitt 1 umfasst das Baufeld 3 mit Rollgasse D3. Dieser Bereich wurde bereits am 31.10.2013 an den Bauherrn übergeben. • Abschnitt 2 betrifft die Baufelder 1 und 4 mit Fertigstellungstermin zum 31.10.2014. Der Auftrag umfasst alle Abbrucharbeiten, den Neubau der Entwässerungskanäle, den Kabeltiefbau und die Leerrohrsysteme, die Flugbetriebsstoffversorgung sowie die Erd- und Deckenarbeiten.
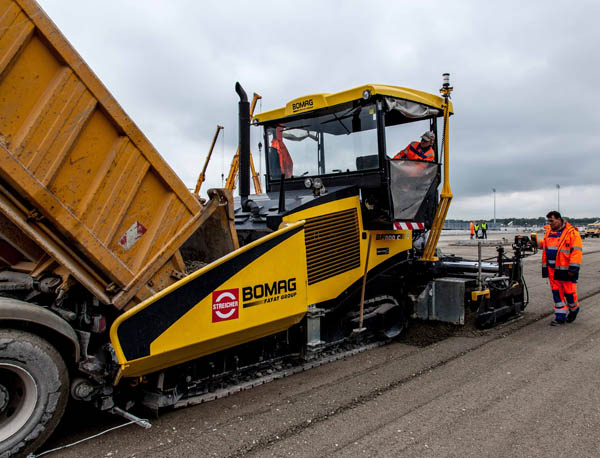
Die Hydraulik des BF 800 C erreichte auf der Münchener Flughafenbaustelle einen niedrigen Kraftstoffverbrauch von durchschnittlich 12,5 l/h.
Das über 100-jährige Unternehmen Max Streicher GmbH & Co. KG aA mit Firmensitz im niederbayerischen Deggendorf beschäftigt an rund 30 Standorten im In- und Ausland über 3.500 Mitarbeiter. Ausgehend vom Tief- und Ingenieurbau hat sich das Leistungsspektrum des Unternehmens in den vergangenen Jahrzehnten stark erweitert und umfasst heute darüber hinaus den Rohrleitungs- und Anlagenbau, den Maschinenbau und den Bereich Roh- und Baustoffe. Zu den Referenzprojekten der vergangenen Jahre zählen im Straßenbau z. B. der Overfly am Autobahnkreuz München Nord oder diverse Fahrbahnerneuerungen auf Autobahnen und Bundesstraßen. Das zweite Unternehmen ist die Berger Holding GmbH mit Hauptsitz in Passau. Auch dieses Unternehmen verweist auf seine mehr als hundertjährige Tradition im Hoch- und Tiefbau und seine Referenzen beim Verkehrswegebau der Autobahn A8, der ICE-Neubaustrecke Nürnberg-Ingolstadt und der Schienenanbindung des Flughafens Berlin-Schönefeld.
Insgesamt wurden 10.000 Meter Kabelschutzrohre und 2.550 Meter Kanalleitungen verlegt sowie die Decken der 71.000 m2 umfassenden Flugbetriebsflächen in Betonbauweise und 5.000 m2 in Asphaltbauweise ausgeführt und 1.250 m Schlitzrinnen eingebaut. Zum Einbau der HGT-Untergrundschicht der Vorfeldfläche setzt die Arbeitsgemeinschaft (ARGE) Streicher-Berger den Fertiger BF 800 C von Bomag ein.
Herausforderungen des Großprojektes Eine der größten Herausforderungen bei der Herstellung von Infrastrukturprojekten ist der Einbau von hydraulisch gebundenen Tragschichten (HGT) in großen Stärken und breiten Lagen. Beim Vorfeld Ost des Flughafens München werden hydraulisch gebundene Tragschichten (HGT) aus einem abgestuften Korngerüst 0/32 aus natürlichen Mineralstoffen wie Splitt, Kies und Sand eingebaut. Als Bindemittel kommt Zement hinzu.
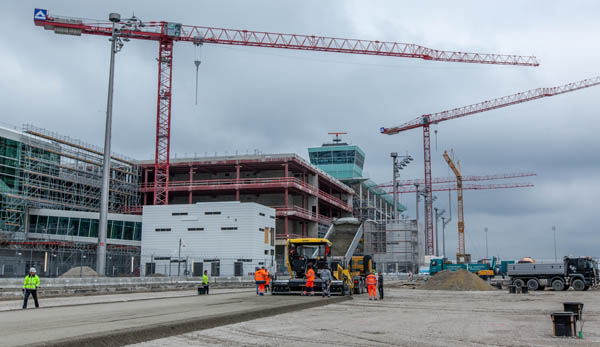
Im Zuge der Erweiterung des Terminals 2 am Flughafen München wurden 76.000 m² Vorfeldfläche in Betonbahnen hergestellt.
Der Kettenfertiger Bomag BF 800 C ist in besonderem Maße für diese HGT-Anwendung geeignet, denn gerade diese Magerschichten stellen höchste Ansprüche an die Belastungen und den Verschleiß von allen Fertigerbauteile, die diesen Materialmix fördern, verteilen und verdichten. Deshalb hat der Fertiger besonders kraftvolle Hydraulikmotoren, die die Kratzerbänder und Schnecken antreiben und gewährleistet so einen optimalen Materialfluss und eine hohe Produktivität, selbst bei diesem kritischen Material. Die Hochleistungsbohle S 500 mit einer Einbaubreite von bis zu fünf Metern ist die schwerste ihrer Klasse und mit Vibration und Stampferleiste ausgestattet. So kann die Bohle nach Herstellerangaben sehr hohe Verdichtungswerte von bis zu 95% garantieren.
Am Flughafen München wird der Fertiger BF 800 C in der Ausführung mit der millimetergenauen Trimble 3D-Fertigersteuerung eingesetzt. Die Arbeitsbreite beträgt fünf Meter und die tägliche Einbauleistung liegt bei etwa 3.000 Tonnen. Die hydraulisch gebundene Tragschicht wird in einer Stärke von 25 Zentimetern eingebaut, die auf 20 Zentimeter endverdichtet wird. Als erhöhte Forderungen an die profilgerechte Lage unter Betondecken sollen +0,5 cm bzw. -1,5 cm Abweichung von der Sollhöhe sowie eine nötige Ebenheit von max. 1,5 cm auf 4,0 m erreicht werden. In einem Abstand von fünf Mal fünf Metern werden später in Quer- und Längsrichtung Kerben angebracht, die als Sollbruchstelle eine unkontrollierte Rissbildung vermeiden sollen.
Mit unkonventioneller Arbeitsweise zum Erfolg „Im ersten Baulos haben wir im vergangenen Jahr auf 24.000 m² den HGT in konventioneller Weise eingebaut“, sagt der Gesamtprojektleiter der ARGE, Walter Weinberger. „Allerdings geschah dies noch herkömmlich mit Draht und Ultraschallsensoren“. Bei dieser Methode werden das Quergefälle und die erforderliche Ebenheit über eine herkömmliche Nivelliersteuerung geregelt. Die Abtastung dazu erfolgt über einen Fahrdraht, der als dünnes Seil gespannt wird und über die auf der gegenüberliegenden Seite bereits fertiggestellte HGT. Diese Nivelliersteuerung arbeitet mit fünf Ultraschallsensoren zur gleichzeitigen Höhenmessung. Die drei Messergebnisse mit der geringsten Abweichung zum ursprünglichen Abgleich werden zur Bildung des Mittelwertes herangezogen. Bei der Seilabtastung zieht der Sensor immer den Schwinger mit der kürzesten Entfernung zum Seil für die Messung heran. Für den Bau der HGT wurden zwei Fertiger, nebeneinander gestaffelt, eingesetzt.
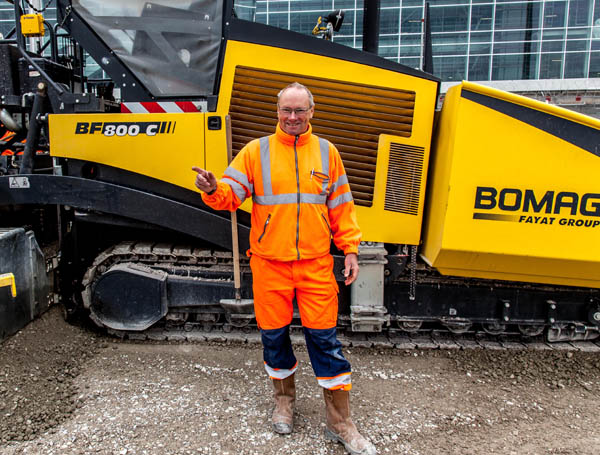
Gesamtprojektleiter Walter Weinberger, Max Streicher GmbH & Co. KG aA, war mehr als zufrieden: Mit dem Straßenfertiger BF 800 C ist seinem Bautrupp eine 30 %ige Zeit- und Kostenersparnis gelungen.
„Irgendwann im November hatte ich die Idee, dass sich das komplexe Profil des Vorfeldes leichter herstellen lassen muss“, erklärt Weinberger und zeigt auf die Fläche vor sich. „Diese Fläche von zirka 34.500 m2 haben wir in exakt 14 Tagen eingebaut. Mit der anderen Methode hätten wir sicher eine Woche länger gebraucht. Die Woche länger braucht man, weil man immer wieder die Fahrbahn testen, Drähte umsetzen und ausmessen muss. So ergibt sich immer wieder viel Leerlauf.“ Das Profil ist natürlich auch komplex – auf der einen Seite hochgebogen bis an die Rinne, dann eine Querbahn und dann wieder hochgebogen und nach Osten wieder abfallend. Dies kann Probleme mit sich bringen, weil immer wieder Eisen umgeschlagen und der Draht umgespannt werden muss. Deshalb wurde auf die schon vorhandenen Daten des 3D-Geländemodells zurückgegriffen. Diese stimmen mit den Daten überein, die auch der Grader für das Vorbereiten des Frostschutzplanums hat. Der Grader fährt ebenfalls mit ATS (Automatische Tachymeter Steuerung) / UTS. Durch die Kombination der Robotik-Funktion mit einem 360°-Prisma ergibt sich der gleiche Komfort wie beim Einsatz eines Fertigers.“
Die Firmen Topcon, Moba, Leica und Trimble bieten solche Schnittstellen für verschiedene Baumaschinen an. Das Prisma wird an eine festdefinierte Stelle des Fertigers gesetzt. Das Tachymeter sendet dann ständig die Positionsdaten des Reflektors an das Funkmodem der Maschine. Dieses leitet die Daten an die Steuerung weiter. Über den Rechner werden das Walzmaß, die Bohlenbreite, die Reflektorhöhe, etc. eingegeben. Damit ist die Bohlenhöhe definiert und der Fertiger kann „drahtlos“ loslegen. Mit dem Einlesen der Daten aus dem CAD-Projekt Vorfeld Ost in die Trimble-Steuerung liegt der Lageplan in Höhe und Fläche vor. Damit kann an jedem Punkt die projektierte Höhe ausgelesen werden und die Bohle fährt selbstständig auf die vorgegebene Höhe.
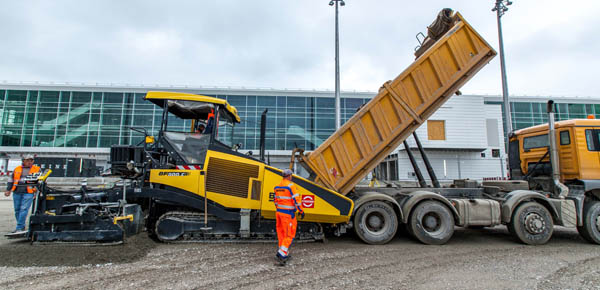
Der HGT-Einbau mit dem BOMAG BF 800 C in Zahlen: 25 cm stark – 5,00 Meter breit – 1.200 m³ pro Tag.
Fotos: www.bomag.com
„Diese Methode setzt voraus, dass man sich vorher über Reaktion des Fertigers informiert hat, denn er braucht fünf Meter, um die Höhe um einen Millimeter zu erhöhen oder abzusenken. Dies ist insbesondere bei einem solchen komplexen Höhenprofil wie dem Vorfeld wichtig“, sagt Weinberger. „Die Herausforderung ist dabei das große Walzmaß bei einer 25 cm starken HGT-Schicht und die strenge Oberflächentoleranz von 5 mm höher und 15 mm tiefer.“ Ein Vermesser mit einer Basisstation und zwei Geräten sorgt für das richtige Maß. Mit einem ATS-Handrover kontrolliert er ständig die Qualität der eingebauten Tragschicht hinsichtlich der Höhe und Lage. Die beiden Funkkanäle beeinflussen sich gegenseitig nicht, da die Maschinensteuerung auf einem anderen Kanal sendet als der Handrover. Mit dieser Vorgehensweise konnte viel Zeit gespart werden: Der Vermesser ist auch bei einem anderen Verfahren notwendig, denn er muss auch hier die Höhe kontrollieren, die Pinneneisen setzen und den Draht spannen und nachjustieren. Die beiden Fertiger haben auch durch das ständige Umspannen und Nachmessen nicht mehr Tragschicht eingebracht als ein Fertiger allein jetzt mit UTS-Steuerung. An einem Spitzentag wurden 1.200 Kubikmeter HGT eingebaut. Die Verdichtungsleistung lag fast immer bei 100%, manchmal konnten auch bis zu 103 % erreicht werden.
Für die Maschinenbediener war das Einbringen mit der Trimble-3D-Steuerung natürlich etwas Neues, wobei sich Polier Hans Kolbinger von der Firma Berger sehr schnell darauf eingestellt hat. „Die Fertiger sind heute alle Menü geführt“, sagt Kolbinger: „Vor zehn oder fünfzehn Jahren war das komplizierter.“
Fazit Mit einem UTS/ATS-gestützten Vermessungssystem werden Fertiger wie der Bomag BF 800 C zu einer hochproduktiven Maschine, die selbst bei hochkomplexen Flächen, wie sie die Flughafeninfrastruktur fordert, noch Zeit und Kosten sparen. Wenn, wie im vorliegenden Fall, der Bauleiter früher selbst vermessen hat, können so bis zu 30 % unproduktive Zeit eingespart werden. Es müssen dann nicht zwei Fertiger drahtgeführt in der Kolonne arbeiten, sondern dies kann nun ein Fertiger übernehmen. Für Maschinenbediener wie Guido Mauermann war die Umstellung auf das neue System problemlos. Vor allem, weil das Team von Berger schon den Tiefbau am Flughafen Berlin-Schönefeld mitgestaltet hat und sich somit in der Materie auskennt. |